Research Projects
Surface segregation in metal alloys in vacuum and gas environments.
Surface segregation is of great importance as it may enhance or suppress desirable and undesirable chemical reactions at the surface. In particular, tuning and controlling surface enrichment by one of the alloy elements is key in developing materials for a hydrogen economy. Driving forces for surface segregation may be different depending on the conditions: the gas environment, temperature, enthalpies of mixing, surface energy, size mismatch of the atoms and the entropy contribution are only some of the parameters that influence the segregation process. A predictive model was developed and applied to Palladium alloys because of their application as storage, catalysts and in membrane reactors for gas separation. In the figure below it is seen that in a H2/CO environment the adsorption of CO on Pd-Ag enhances the segregation of Pd.
Developing stable thin film material for hydrogen gas separation membranes and sensors
Developing stable thin film metal layers on a support for gas separation or sensors that can absorb large amounts of hydrogen without failing is challenging. Hydrogen absorption is accompanied with large volume changes that lead either to embrittlement of the metal layer or delamination from the substrate. By tailoring the thin film’s nanostructure by adapting the magnetron sputtering deposition conditions a stable material was developed and lead to the so-called brush-membrane concept. The open morphology of a brush-membrane enhances stability and kinetics of hydrogen uptake.
A 100 nm Pd layer on oxidised silicon. The brush - membrane consists of loosely bound columns separated by nano-voids.
Applying an appropriate intermediate layer can also prevent delamination and embrittlement, as can be seen in the images below.
Optical microscopy images of 100 nm thick Palladium magnetron sputtered layers after one hydrogen loading - deloading cycle: (left) Pd on an oxidised Si-wafer with an intermediate layer of polyimide and (right) Pd on oxidised Si without intermediate layer. The compressive stress when hydrogen absorbs causes film buckling. Pd nanostructure and intermediate layer choice can prevent layer failure.
Self-Healing Thermal Barrier Coatings for Prolonged Lifetime
This project deals with the creation of a new, unique self-healing thermal barrier coating (TBC) for turbines and other thermally loaded structures in order to realize a significant extension of the lifetime of critical high-temperature components. The concept is based on novel Al2O3 coated MoSi2 particles embedded in the TBC layer, typically consisting of yttria-stabilized zirconia (YSZ); see Figure. As the current TBCs do not exhibit any self-repair, the new self-healing TBC will offer a reduction of the number of TBC replacements during an engine lifetime and enhance the reliability of the critical components.
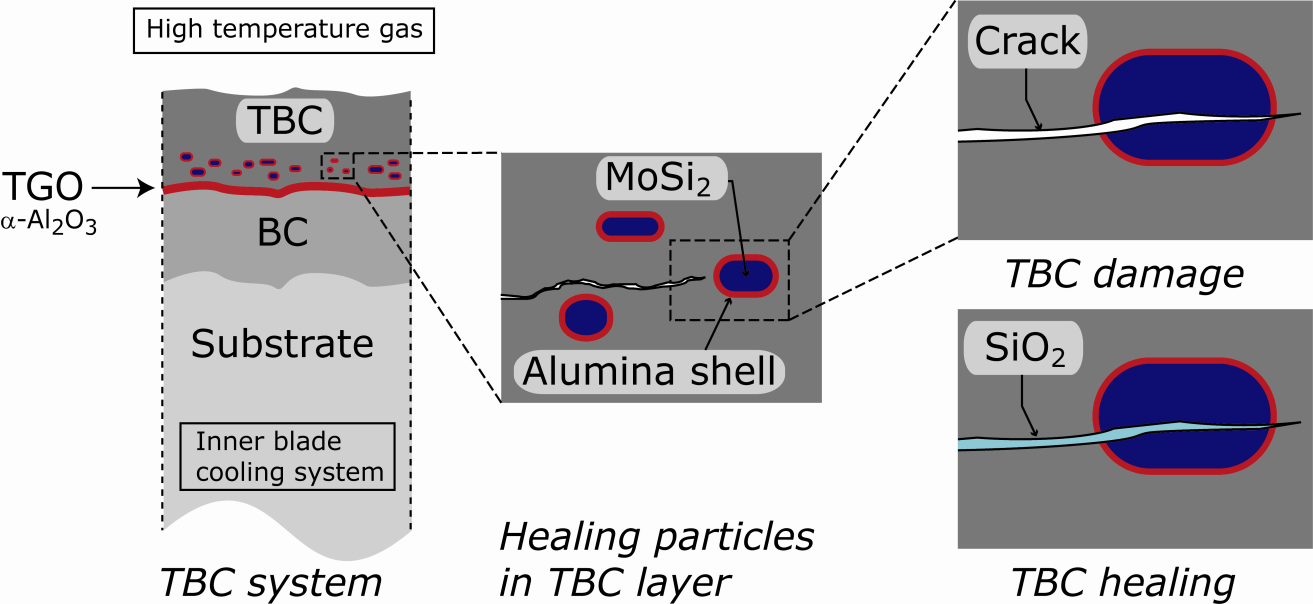
Figure Schematic of crack-healing mechanism in a thermal barrier coating (TBC) with encapsulated Mo-Si based particles. The TBC system comprises a superalloy substrate with a bond coating (BC), which produces a thermally grown oxide (TGO) during service, and the modified yttria-stabilized zirconia (TBC). Upon oxidation of a cracked Mo-Si based particle, silica (SiO2) fills the crack over a long distance.
The principle of the crack healing with particles containing Mo-Si is based on the formation of SiO2 by oxidation when such a particle is exposed to the ambient gas at high temperature through a crack in the TBC. The Mo forms a volatile oxide (MoO3) and leaves the coating via crack path, while simultaneously SiO2 fills the crack and close it, thereby restoring the integrity of the TBC system. However amorphous SiO2 is not enough to achieve a durable structure in the YSZ matrix. Herein formation of ZrSiO4 occurs as a result of SiO2 reaction with YSZ and enhanced the durability of the healed cracks. This mechanism postpones the failure of the TBC system. However, since oxygen can readily diffuse through the YSZ matrix and the porous nature of the coating, MoSi2 tends to oxidize prematurely, before damage occurs. To prevent this, the healing particles must be encapsulated.
<link typo3 www.sambaproject.eu _blank>www.sambaproject.eu
Self-Healing Oxide Ceramics
In oxide ceramics (e.g. Al2O3, 3Al2O3·2SiO2, ZrO2·xY2O3), the crack healing efficiency depends on concentration and size distribution of the healing particles made of e.g. TiC or SiC. The relations between these parameters and the strength recovery of self-healing ceramics are determined. Oxide ceramics with different concentration and distribution are produced and tested on crack healing and strength recovery for various damage levels. The crack filling kinetics as a function of temperature, time and environment of the self-healing oxide ceramics is studied. To promote the transition of these self-healing ceramics into industrial praxis, the results of this research must eventually lead to model-based guidelines and design rules to manufacture these self-healing ceramics.
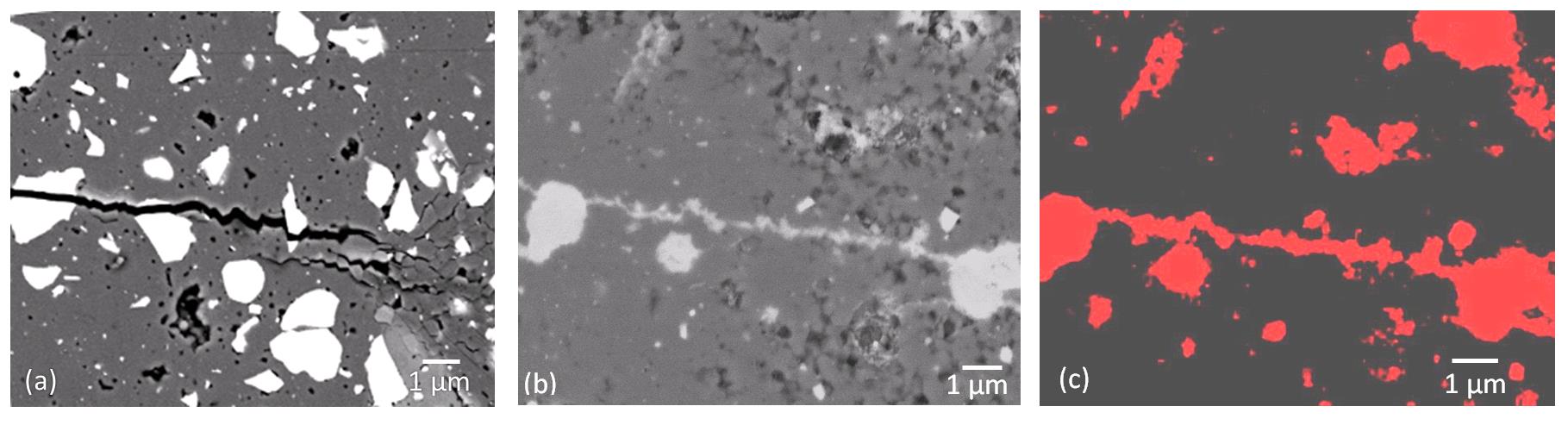
SEM micrographs of Al2O3/TiC composite (a) close-up showing crack-particle interaction (b) filling of a crack with TiO2 and (c) X-ray of Ti mapping in the filled crack
MAX Phases: Synthesis, Structure and Properties
In contrast with many other common engineering ceramics, MAX phase metallo-ceramics are tough and therefore damage tolerant. The MAX phase ceramics are stable up to high temperatures and corrosion resistant. The high thermal conductivity makes these ceramics thermal shock resistant. Their static strength is maintained up to high temperatures, above which creep will become the limiting factor. Also MAX phase materials are easy machinable. These properties make MAX phase materials attractive for high temperature applications, where the material is exposed to thermal cycles, mechanical loading and oxidation.
The unique combination of mechanical, thermal and electric properties of MAX phase material is due to their atomic layered and hexagonal crystal structure; see Figure. The general formula is Mn+1AXn, where n equals 1, 2 or 3, M is an early transition metal, A is an A group element (mostly IIIA and IVA, like Al and Si), and X is C and/or N.
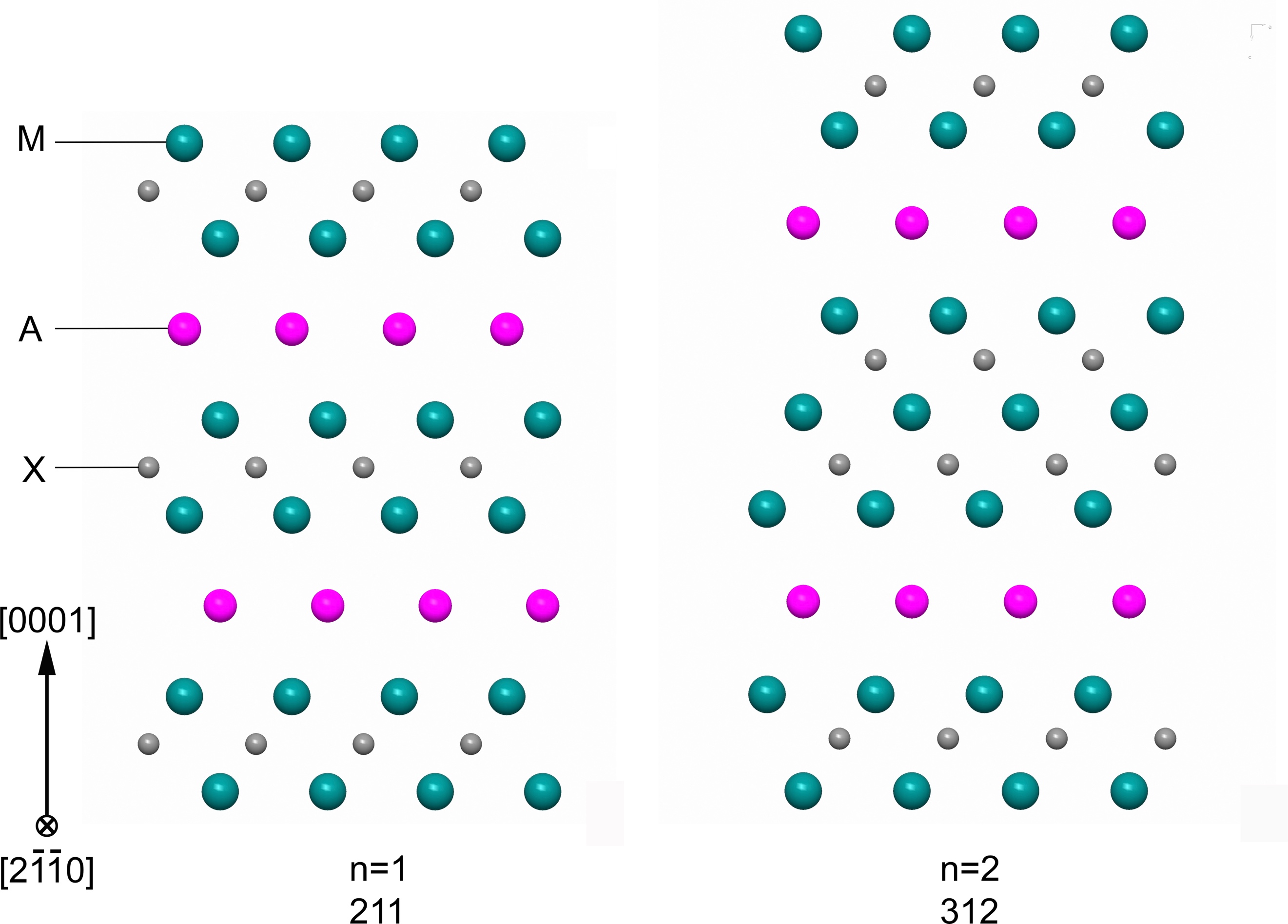
Figure Atomic layered structure of hexagonal closed packed Mn+1AXn phases.
Recently, it has been demonstrated that crack damage in Ti3AlC2, Ti2AlC and Cr2AlC MAX phases can be healed by selective oxidation of the A element; see Figure. Hence, the MAX phase is part the healing reaction and the healing product is formed by consuming oxygen from the gas atmosphere.
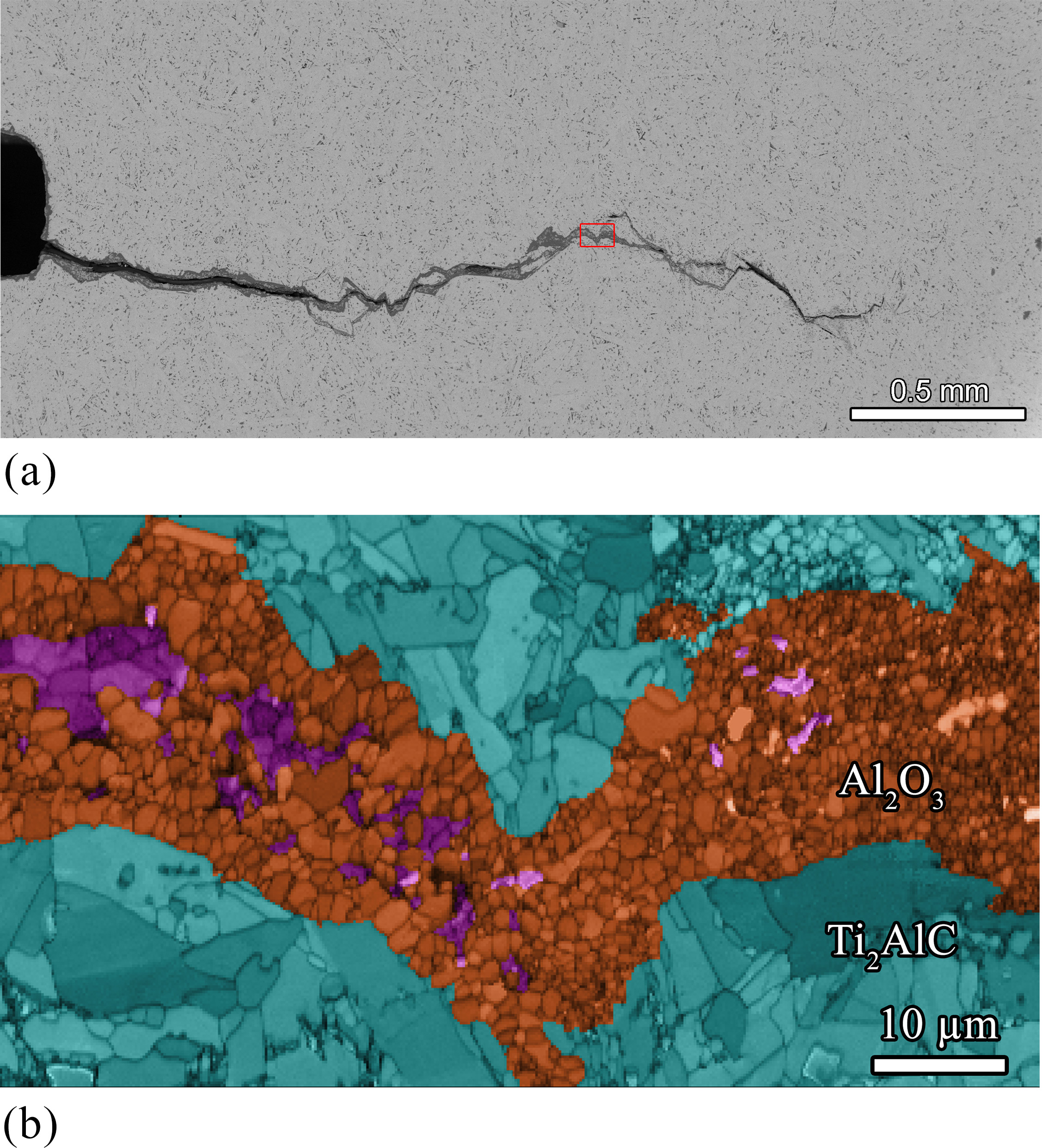
Figure Crack in Ti2AlC repeatedly healed by oxidation at 1200 ºC for 2 hours in air. (a) An overview of the crack after 7 fracture and healing cycles. (b) Detailed micrograph of the area indicated in (a), obtained with scanning electron microscopy (SEM) using electron backscatter diffraction (EBSD). The oxides in a healed crack consist mainly of a-Al2O3 (orange) and some TiO2 (purple).
The research aims at quantitative determination of the crack filling kinetics and strength recovery of selected MAX phase ceramics as a function of temperature, time and environment. To transfer this academic research to pre-industrial exploration of this material in practical applications, models are developed which quantify the degree of restoration of the initial mechanical properties as a function of the operating temperature and time.
With in situ 4D (time-lapse) X-ray tomographic imaging the temporal evolution of local crack opening and healing was captured during multiple cracking and autonomous repair cycles at a temperature of 1500 K. A specialized thermomechanical setup was coupled to a synchrotron X-ray tomographic microscopy end station at the TOMCAT beamline in Switzerland at the Paul Sherrer Institute. For the first time, the rate and position dependence of crack repair in pristine Ti2AlC material and in previously healed cracks has been quantified.
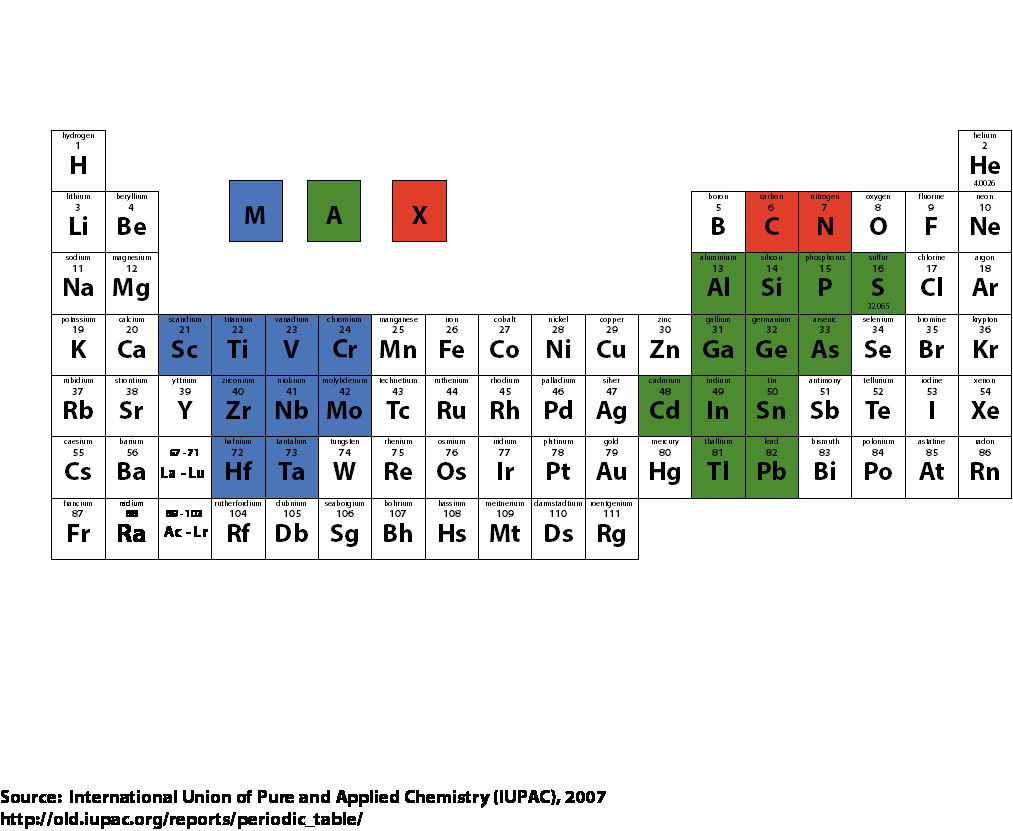
Figure Periodic table with is Mn+1AXn phase components
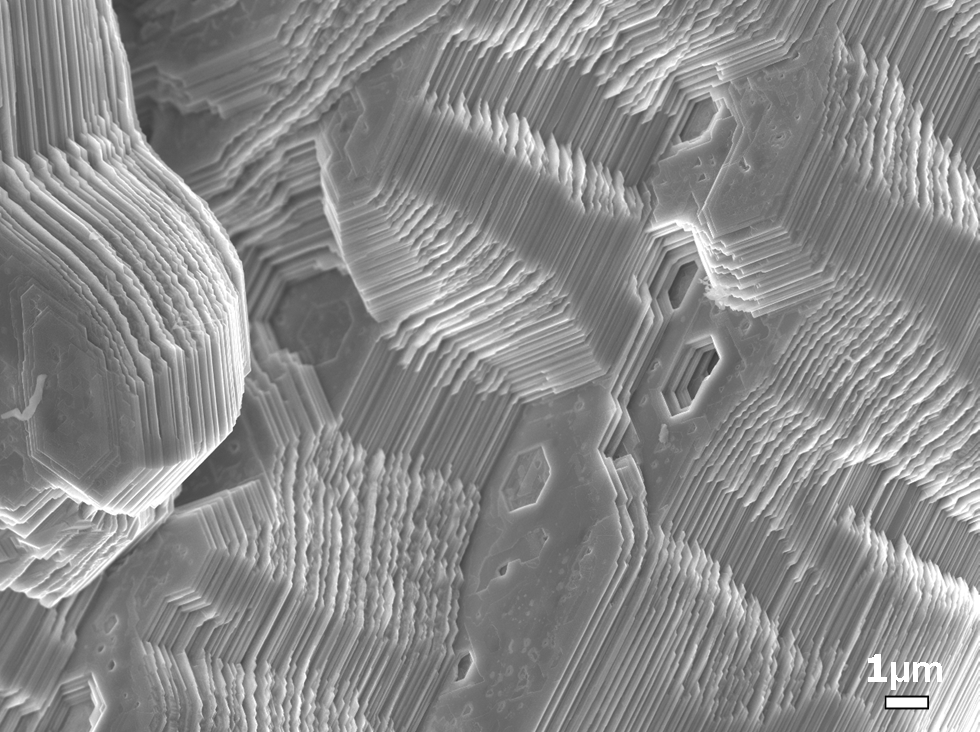
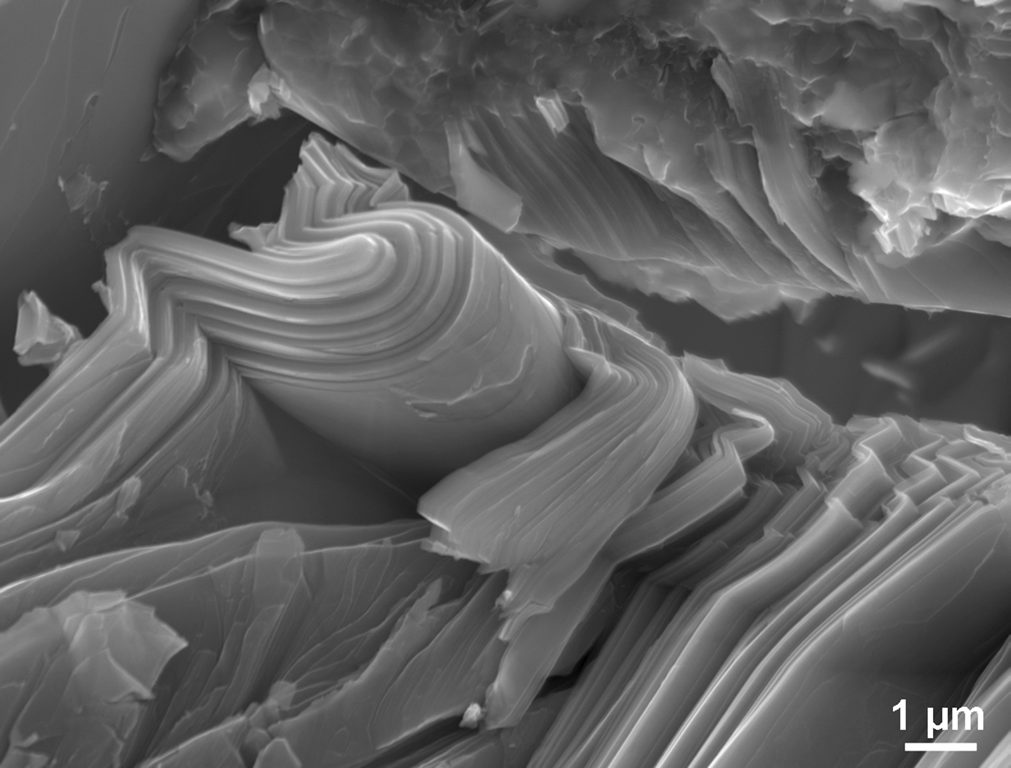
Figure Fracture surface of MAX phase showing laminar structure and kink bands
Oxidation Phenomena of Advanced High Strength Steels
This project aims to define the annealing process windows for advanced high strength steel (AHSS) composition and as such will focus on developing a novel multi-element and multi-variant 2D/3D model for the selective oxidation and reduction of high strength steel sheets. In order to include the role of processing history (i.e. both hot and cold rolling) of the AHSS and thus their microstructure and predict nucleation and growth of internal and external complex oxides necessitate modelling in 2 or 3 dimensions. Experimental work is necessary to collect vital thermodynamic and kinetic data, and validate the model calculations.
The alloying elements of these high strength steels in particular results in the formation of stable oxides at the surface, which leads to poor wettability and adhesion when galvanising. By developing a continuous annealing process in which combined internal selective oxidation and reduction of the oxides in the steel alloy surface occurs, the presence of oxides at its surface may be avoided prior to galvanising.
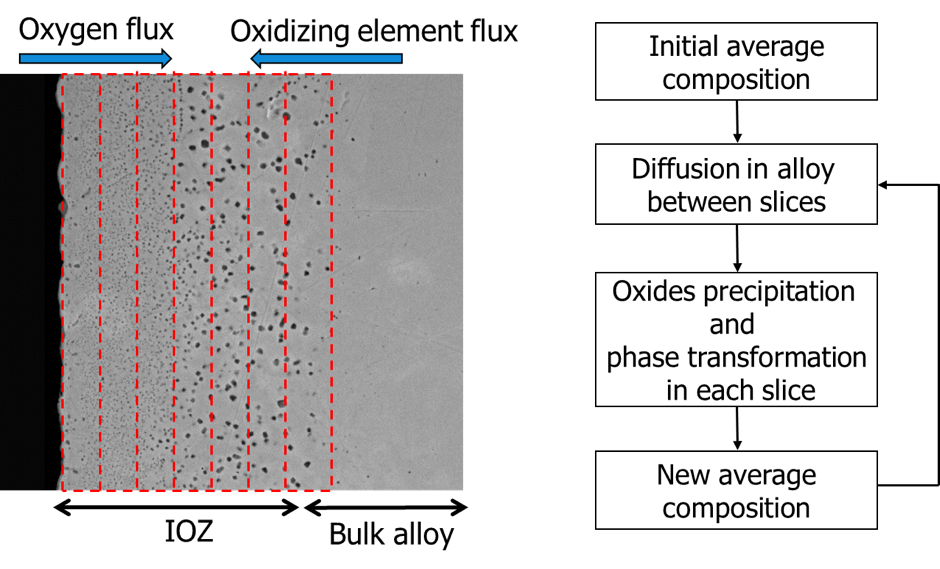
Figure Schematics of the internal oxidation model and the flow chart of the model’s operation
ZnMg- coatings for the Next Generation Steels” is driven by the desire to develop PVD continuously coated strip as a breakthrough technology for depositing anti-corrosion ZnMg coatings on NGS strip. It aims at understanding how the adhesion property of PVD ZnMg coatings on NGS is influenced by PVD including the subsequent thermal processes, and by the chemical composition and microstructure of the coating and substrates. These parameters are used to predict the mechanical performance of substrate-coating systems during subsequent thermal and forming operations by micromechanical simulations. The ultimate goal is to solve the adhesion problem of novel PVD ZnMg-based multilayer coated NGS by optimizing the coating design and interface structure, and enhancing interfacial bonding through hybrid ion implantation and thermal activated intermetallic reactions, and/or by employing an adhesion interlayer.
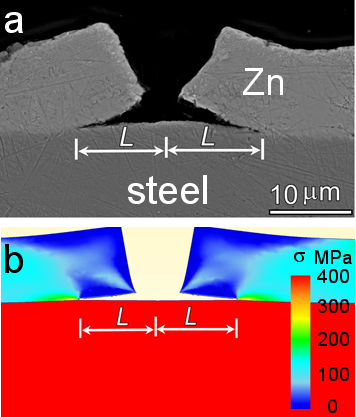
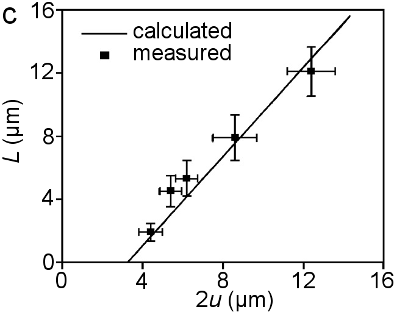
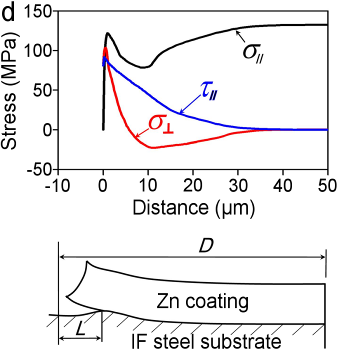
Figure In-situ SEM observation of Zn coating cracking under tension (a) and simulation (b); (c) measured interface crack length (L) as a function of the crack gap (2u) for a galvanized IF steel, together with the calculated result for a coating adhesion strength of 180 MPa; (d) stress distribution near the crack tip.
Development of Advanced Methods for Characterization of Materials
A novel wedge splitting test (WST) is under development to accurately measure the strength and toughness of ceramics. This work is done in conjunction with fracture mechanical modeling using finite element simulations. During the tests, the crack growth is observed with optical as well as acoustic emission techniques, while monitoring the load and displacements. This project aims at quantifying the materials properties after healing of crack damage.
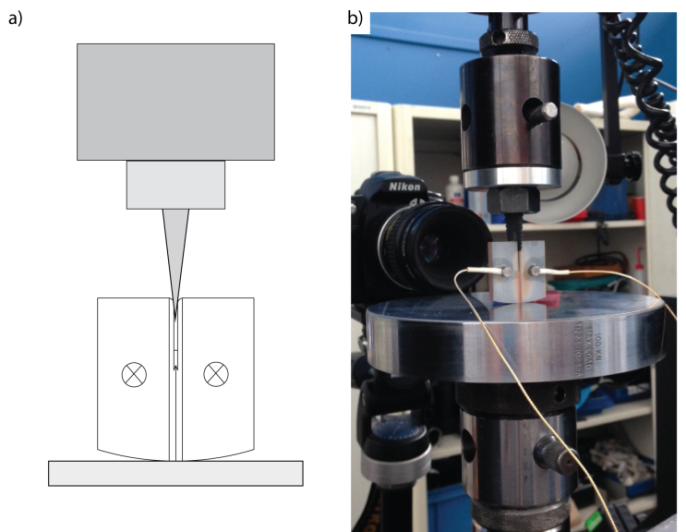
Figure Test setup of wedge loaded chevron notched specimen with microphone positions indicated (a) schematic and (b) actual test setup.
The so-called wedge and Brazilian nut tests have been developed to create a controlled crack (i.e. without total fracture). These tests allow for the determination of the mechanical properties (strength and toughness) of pristine and healed material. For designing the sample geometries and evaluation of the experimental data (load versus displacement) a finite element code based on elasto-plastic material behaviour and fracture mechanics is developed. Machining of the special sample geometries out of the self-healing ceramics was done by Ceratec (associate partner).