Disassembly: Essential to repair
Each time Bas Flipsen joins the Repair Café in his hometown, he comes across screws that are difficult to access because they are hidden deeply within a product. ‘I recommend anyone who wants to become a circular practitioner, students and professionals alike, to spend time at a repair café’, he says. ‘It will give then first-hand experience at how poor product design impedes repair.’ It is one of the reasons why he spends much of his research time on understanding disassembly and creating valuable tools that help guide product (re)design.
A clever map for disassembly
‘No matter the circular strategy, it is vital that a product is easy to disassemble’, Flipsen says. ‘A Disassembly Map provides an intuitive visual representation of a product’s architecture, allowing designers to identify design features that hinder repairability.’ The visualisation not only considers the sequence of disassembly to reach a certain component, it also takes into account the time and type of tools needed, and whether the fasteners (such as screws and bolts) can be reused during reassembly or need replacing.
A Disassembly Map can also be used to redesign products. To increase the repairability of a product, for example, the components that are the most likely to fail should be the easiest to access for repair or replacement. This design strategy is called surfacing. ‘Basically, you bring such a part closer to the surface, thereby reducing the number of steps needed to reach it,’ Flipsen says. ‘For instance, you shouldn’t have to spend a few hours replacing a fuse worth ten cents.’ Next to surfacing, the Disassembly Map may also suggest merging various non-essential components into a single, easy to remove module (called clumping) or to save time by reducing the number of fasteners used to fix a certain component (called trimming).
Hotspot Mapping: pinpointing repair design
Obviously, not all components can be easily accessible, nor are they all equally important when it comes to repair or any other circular strategy. This is where Hotspot Mapping comes in, which helps guide designers in focussing any (re)design efforts for repair. ‘Traditional repairability assessment methods focus on failure-rates and functionality of components’, Flipsen says. ‘Next to these priority parts, it was our goal to also consider the embodied environmental impact and economic value of the various components.’ The time and strength needed to reach a certain component are also part of Hotspot Mapping. After all, a valuable and still-functioning part buried deeply inside a broken product is hard if not impossible to repair and basically lost as donor part.
A starting point for both Disassembly Mapping and Hotspot Mapping is an existing product, which is completely taken apart. Applied in combination, they point designers towards parts in the product architecture which are most critical for ease of disassembly, while also providing guidance on how to redesign the product. ‘We provide masterclasses for professional designers and offer it to students as an elective master’s course.’
Printed spare parts
Flipsen’s research extends beyond direct product design. Take 3D-printing, a modern technology that at first thought seems ideal for custom-creating spare parts that are not or no-longer available. ‘As part of the EU-funded Sharepair project, we looked into its viability in a repair café setting’, he says. ‘But without access to the digital 3D model of the broken part, it turned out to be too cumbersome a solution.’ Its application was also limited because of various quality requirements, such as heat resistance, food safety and mechanical strength. ‘You simply can’t replace a metal drill cog with the plastics used for 3D printing. There is a reason why the original cog broke.
But he hasn’t given up on the idea and is currently looking into how 3D-printing for repair may be of benefit to companies themselves. There is currently legislation underway stipulating how long a period of time spare parts must be available. ‘Long-term storage of spare parts is costly and a waste of materials if they are not used’, Flipsen says. But what about the printing of metal parts? ‘Professional metal and powder-bed printers could meet quality requirements and provide instant delivery simply by mailing the digital 3D model of the part, thereby lowering the need to stock spare parts.’ Later on in this white paper, Jan van Os discusses ATAG’s efforts into 3D printing of spare parts for kitchen appliances.
A shift in repairability thinking
It appears as though an increase in repair legislation will lead to a shift in product design, in business models and in consumer perception. Some of these shifts are already visible, for example in service-based business models. ‘You can now lease high-end headphones’, Flipsen says. ‘Because the company owns the product, they have a strong incentive to keep it functional.’ This is reflected in the headphone design, with some headphones having modular parts so the consumer can easily repair the headphones at home. The company only needs to mail the customer the replacement component. ‘Likewise, companies leasing bicycles to students were quick at redesigning these bikes to reduce failure rates and allow efficient servicing.’
When it comes to facilitating sustainable consumption, Flipsen also foresees a great future for Urban Resource Centres – a combination of a Fab Lab (a small-scale workshop offering personal digital fabrication), a second-hand store and a recycling centre. ‘You enter with something that is broken, and never leave without a working product. If they cannot repair it, you can buy a second-hand replacement for little money. The broken product will be used for spare parts or will be recycled. In the future, these may also feature advanced 3D printers for the on-site manufacturing of spare parts.’
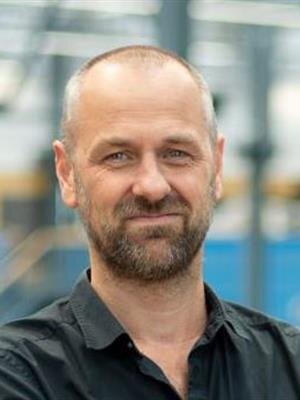
Bas Flipsen
- +31 (0)15 27 89398
- s.f.j.flipsen@tudelft.nl
-
Room 32-B-3-090
Present on: Mon-Tue-Thu-Fri
"Leave tracks, no traces."