Brushless electric starter/generator for aerospace
Brushless Permanent Magnet electric starter/generator for aerospace applications
Brushless Permanent Magnet electric starter/generator for aerospace applications
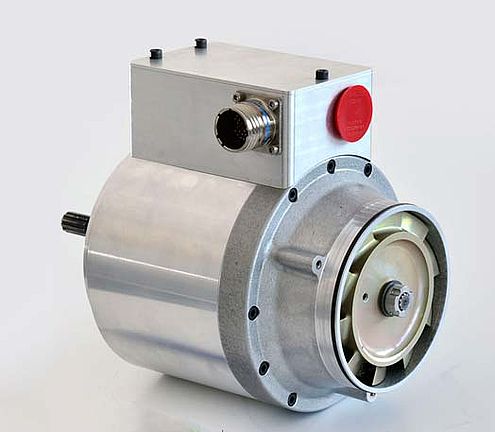
Project description
The gas turbines in smaller aircraft are often started with electrical starter/generators. Historically, brushed dc-machines are used. While these are simple to control, the brushes require periodic maintenance, increasing the operating cost of the aircraft. This project explores the possibilities of using high-speed permanent magnet synchronous machines as alternative to the brushed dc-machines.
The design of this starter/generator is driven by three aspects: starting torque and duration, generator torque and speed range and safety considerations. These objectives conflict and pareto based multi-objective optimization is used to gain insight into the machine capabilities. Throughout the entire design process, finite element analysis and highly detailed lumped element models are used to analyze machine performance with both high accuracy and flexibility. Special attention is paid to efficiently using FEA to minimize computational effort without sacrificing accuracy.
In addition to the basic machine design, critical aspects such as winding AC losses, rotor losses, machine performance and losses during faults, fault detection, and failure behavior are studied with great detail using a mixture of FEA and experimental validation.
This project is a collaboration between Delft University of Technology, Aeronamic B.V and the Dutch National Aerospace Laboratory (NLR), and received funding from the European Union’s Seventh Framework Programme (FP7/2007-2013) for the Clean Sky Joint Technology Initiative.