Researchers create a new class of rate-sensitive mechanical metamaterials
Researchers at the Department of Biomechanical Engineering of Delft University of Technology have created a new class of metamaterials that can dynamically switch their mechanical behaviour. It may form the basis for practical applications such as fall-protective clothing for the elderly. The results are to appear in the journal Science Advances on 17 June.
Metamaterials are artificially crafted material structures that derive their properties from their internal microstructural design, rather than the chemical composition of the material they are built up from. Metamaterials can be designed to show exceptional properties not found in simple natural materials. For example, while structures that are compressed in one direction are intuitively expected to expand in the opposite direction, a class of metamaterials called auxetic materials are purposefully designed to do the opposite.
Mechanical metamaterial functionalities
Thus far, mechanical metamaterial functionalities have not exploited time-dependent effects. This is surprising, says Dr. Shahram Janbaz, researcher at the Biomaterials & Tissue Biomechanics group of TU Delft and first author of the paper, because a lot of flexible materials used to construct mechanical metamaterials, such as polymer-based plastics, show mechanical behaviour that depends on the speed with which they are deformed. “Viscoelastic materials, when strained, undergo slow changes that dissipate energy. Their mechanical response, therefore, depends on how fast you deform them.”
The team, led by Prof. Amir Zadpoor, now brings the time dimension into the mechanical metamaterial toolbox, creating what could be considered a new class of metamaterials that can dynamically switch their mechanical behaviour.
The team constructed tall pillars that consist of two different materials: one side is made from a material that responds to the speed of deformation while the material of other side does not care about how fast it is deformed. When applying a compressive force along the long axis direction of this “bi-beam”, the elasticity of both materials ensures that it doesn’t break but rather buckles.
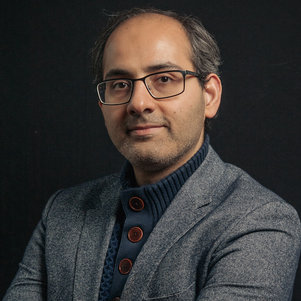
A.A. Zadpoor
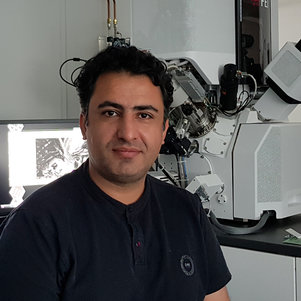
Strange properties
The researchers showed that the bi-beam predictably buckles to either the left or the right side depending on the speed of compression. This strain rate-dependent behaviour of bi-beams is the key to creating new materials with strange properties not seen before. “All you need to do is to find a clever way of assembling bi-beams and odds are pretty good that you find mechanical behaviour that has never been reported before”, says Zadpoor.
Janbaz: “For example, we connected two parallel, mirrored bi-beams to each other through stiff connectors as a basic unit cell that can be repeated in all directions to create a three-dimensional metamaterial lattice structure. We found that, by increasing the strain rate, the mechanical behaviour of such a cell switched completely from auxetic to conventional.” Videos accompanying the publication show how a lattice made up of interconnected unit cells shrinks for low compression speeds and expands for high speeds.
Applications
One of potential applications of metamaterials showing such switching behaviour is that of protection against falls. Zadpoor: “Imagine a wearable layer. Under normal circumstances, it is soft and follows the movements of the body. When an impact occurs, the material switches its behaviour, acting as a shock absorber”. This might help people suffering from osteoporosis, where bone fractures constitute a major complication.
The researchers also created bi-beam lattices that are programmed to become less stiff if they are strained more quickly. This behaviour can be called negative viscoelasticity and has not been observed before in solids.
While it might be difficult to create much smaller bi-beams of the same design as the centimetre-sized model systems tested here, the researchers see possibilities to use 3D printing techniques to create lattices of tiny bi-beams.
The researchers are excited about the potential of their bi-beam design. “We expect that this basic element can be used to create a rich variety of mechanical behaviours,” says Janbaz.