Compliant mechatronic systems with high numbers of individual transducer elements could be useful for various complex distributed sensing and/or actuation tasks in industry (e.g. handling fragile silicon wafers), military (e.g. compliant robots) and medicine (e.g. drug-delivery). Often such systems are impractical to implement due to high total cost of laborious engineering, numerous components and time-consuming assembly process. To a significant extent these limitations can be overcome by using distributed (‘smart’ material) transducers instead of the conventional ones. Entire mechatronic systems can be realized by etching its individual transducers and components into a monolithic ‘smart’ material substrate. However, the today’s ‘smart’ materials also come with their challenges, both in actuation and sensing phenomena. Frequently the smart materials are proposed for application where conventional transducers significantly outperform them, while no attention is paid to distributed mechatronic systems that are difficult to design, construct and miniaturize with conventional transducers.
This research focuses on different aspects of realizing distributed compliant mechatronic systems using monolithic ‘smart’ material substrates. The individual studies seek to improve the available sensing and actuation methods, and investigate application of etching, cutting and deforming techniques on smart materials to obtain novel active distributed 3D structures.
PI (team)
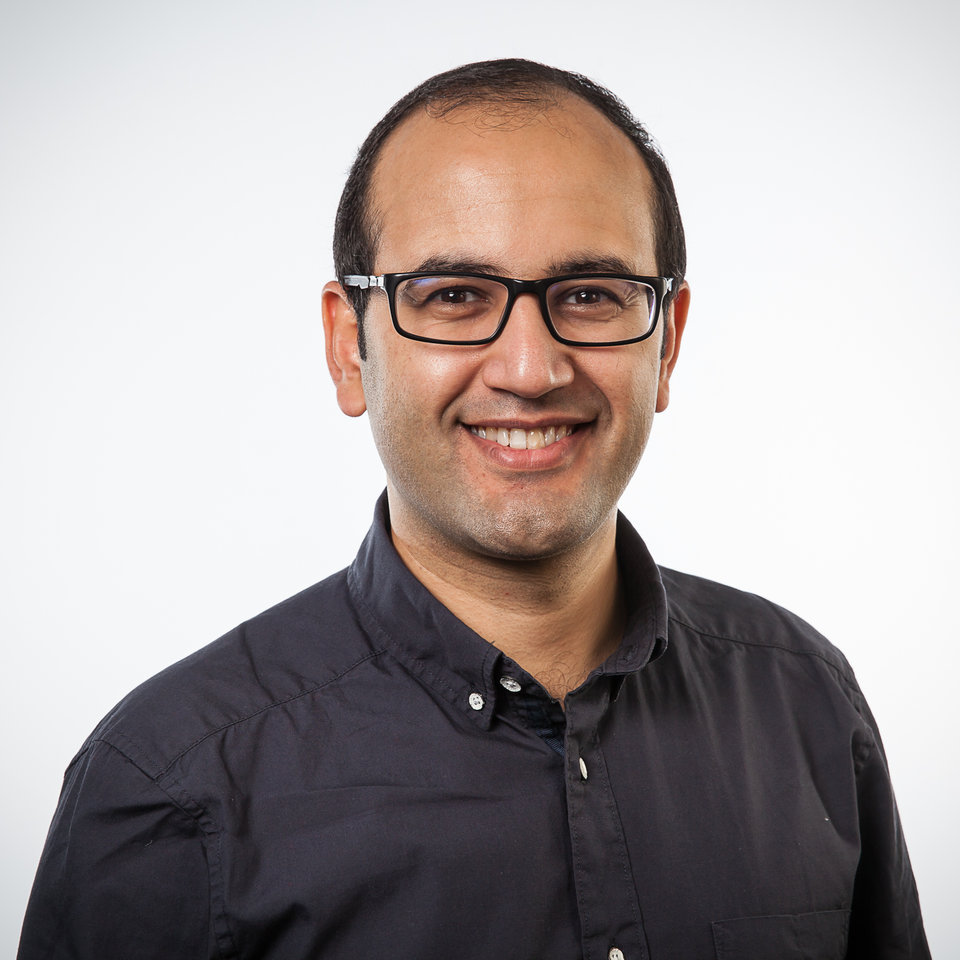
Hassan Hossein Nia
TU DelftPhD / PostDoc
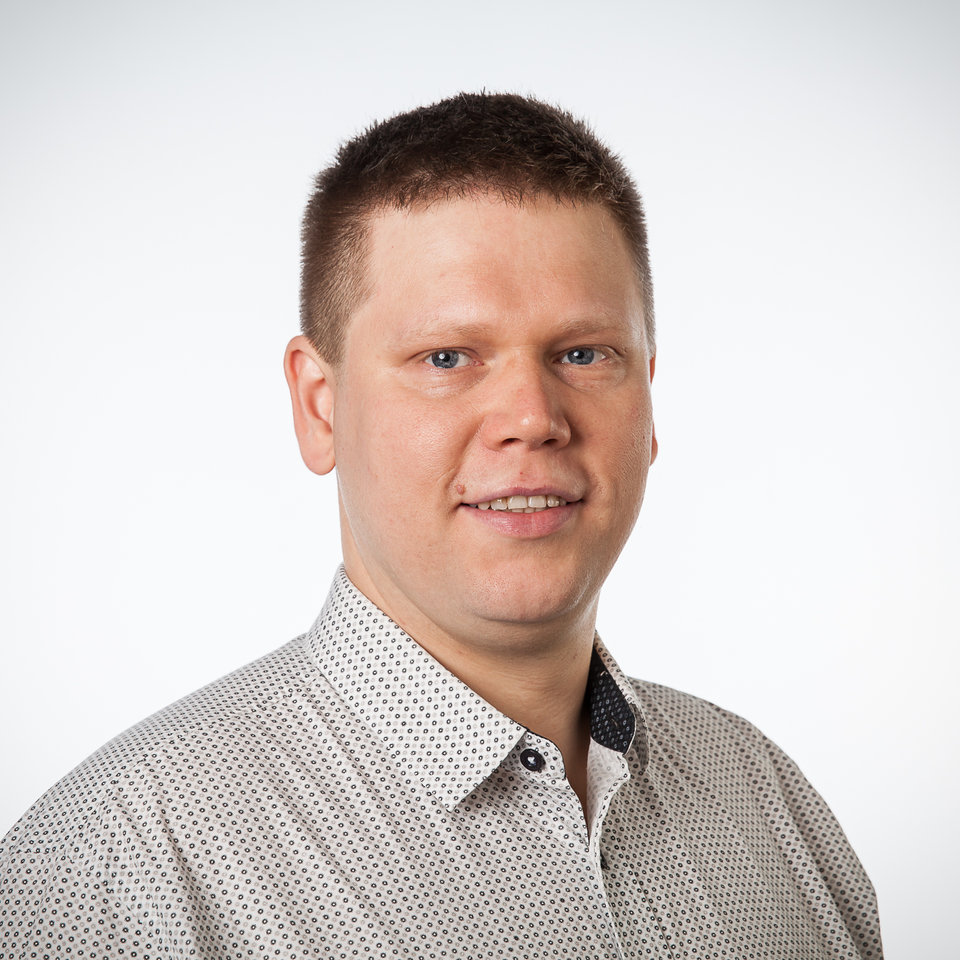
Andres Hunt
Postdoctoral Researcher, TU Delft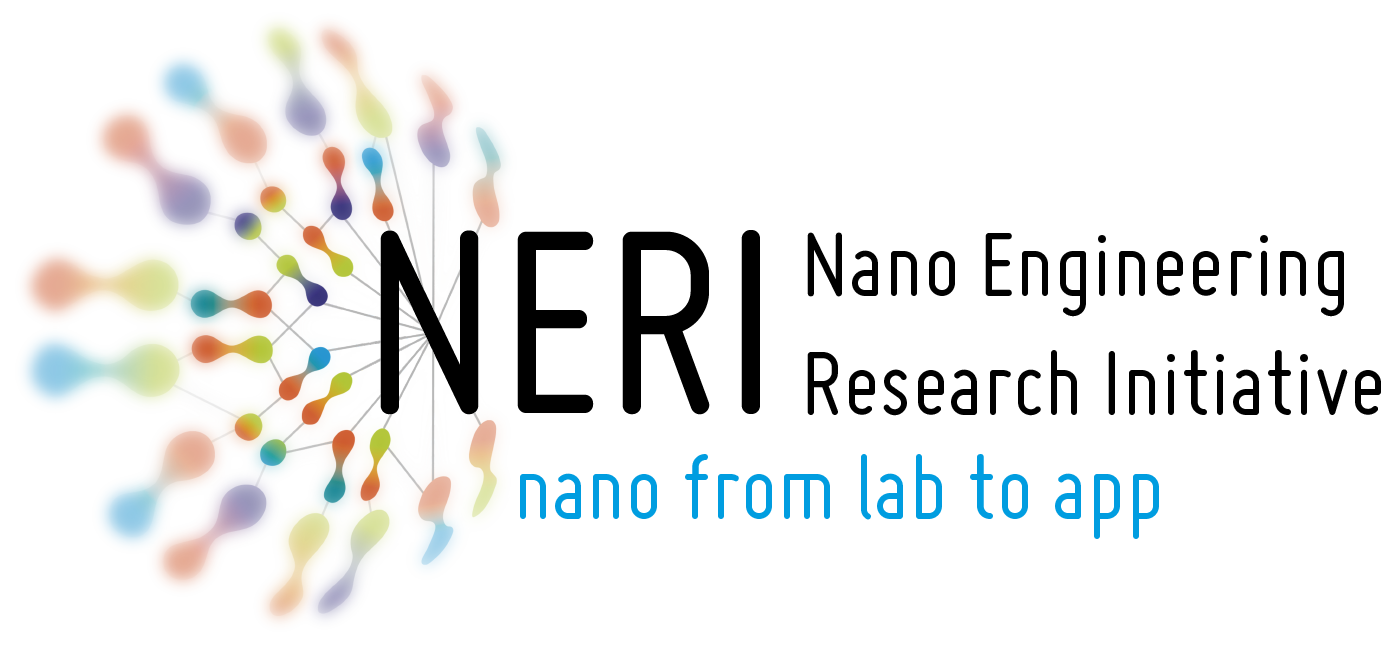