Many applications for Functional Material Structures (FMS) require some sort of actuation of the material to deform it and do some work. In order to design suitable FMS for actuation, the right incorporation and placement of actuators, suitable physical principles of actuation, manufacturing options and constraints and limits on application must be considered. The different options for actuation are categorised and the ‘ideal’ form of implementation was formulated for semi static and dynamic situations providing a guideline for the design of active FMS.
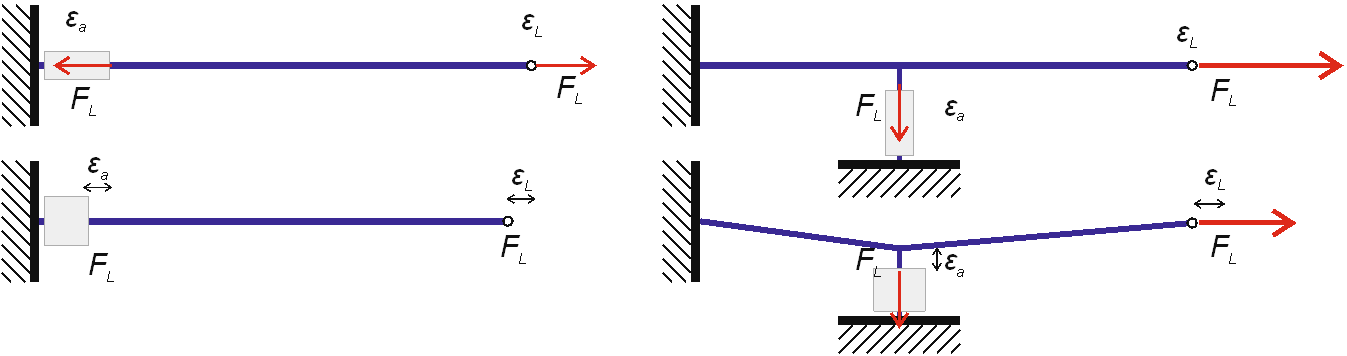
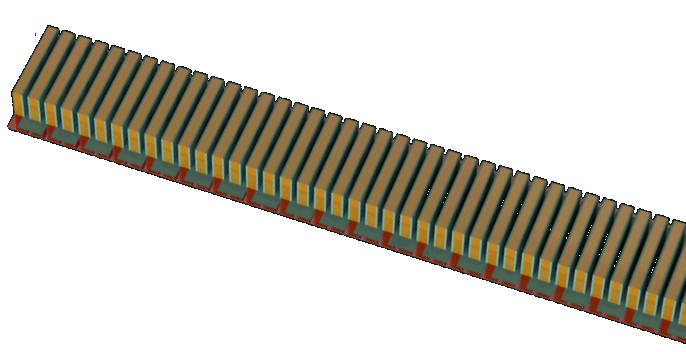
PI (team)
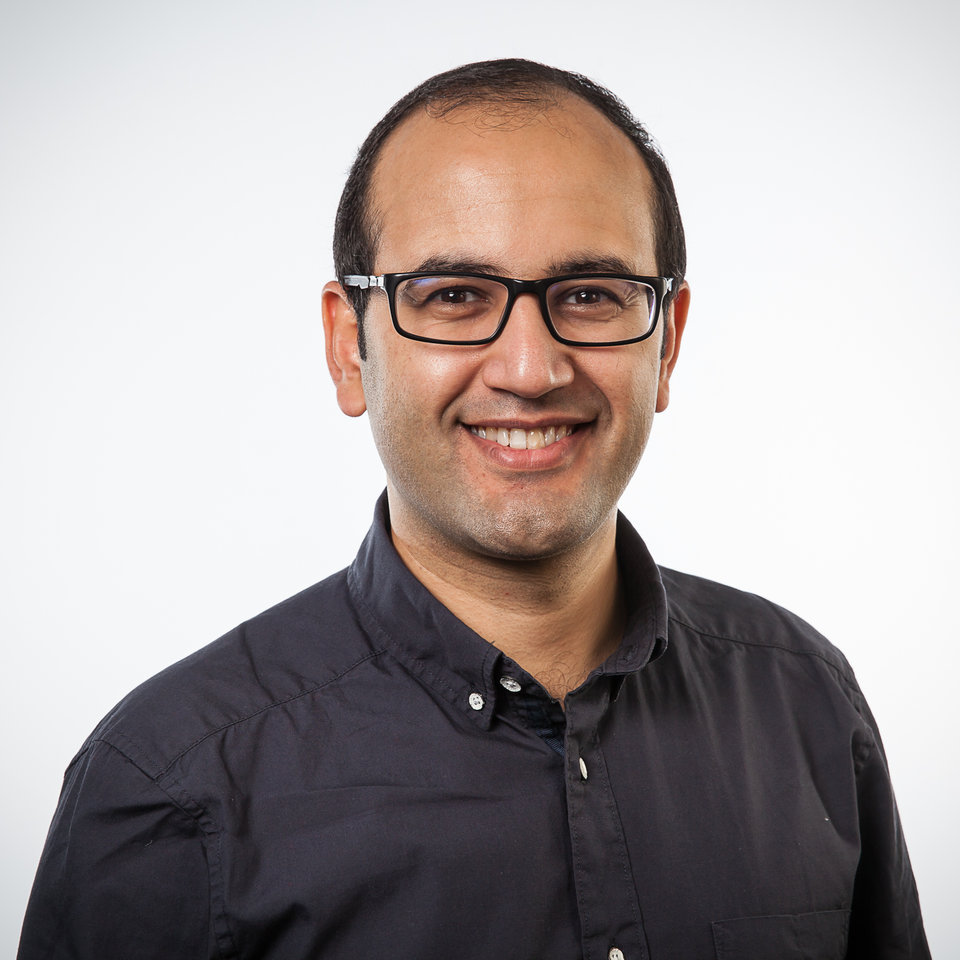
Hassan Hossein Nia
TU Delft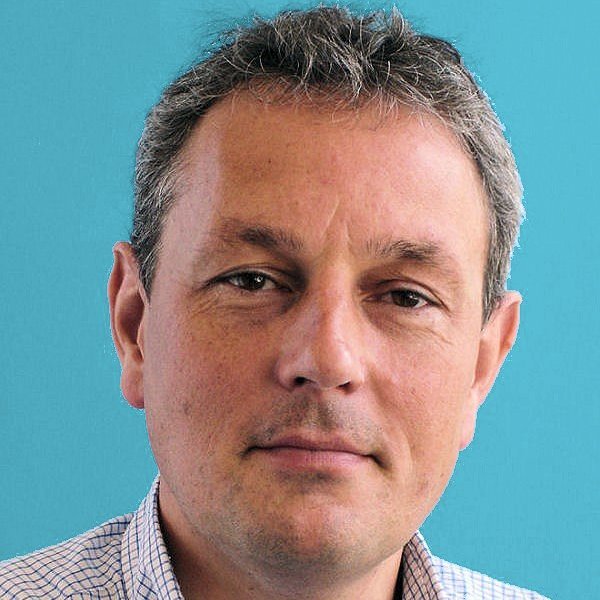
Fred van Keulen
TU Delft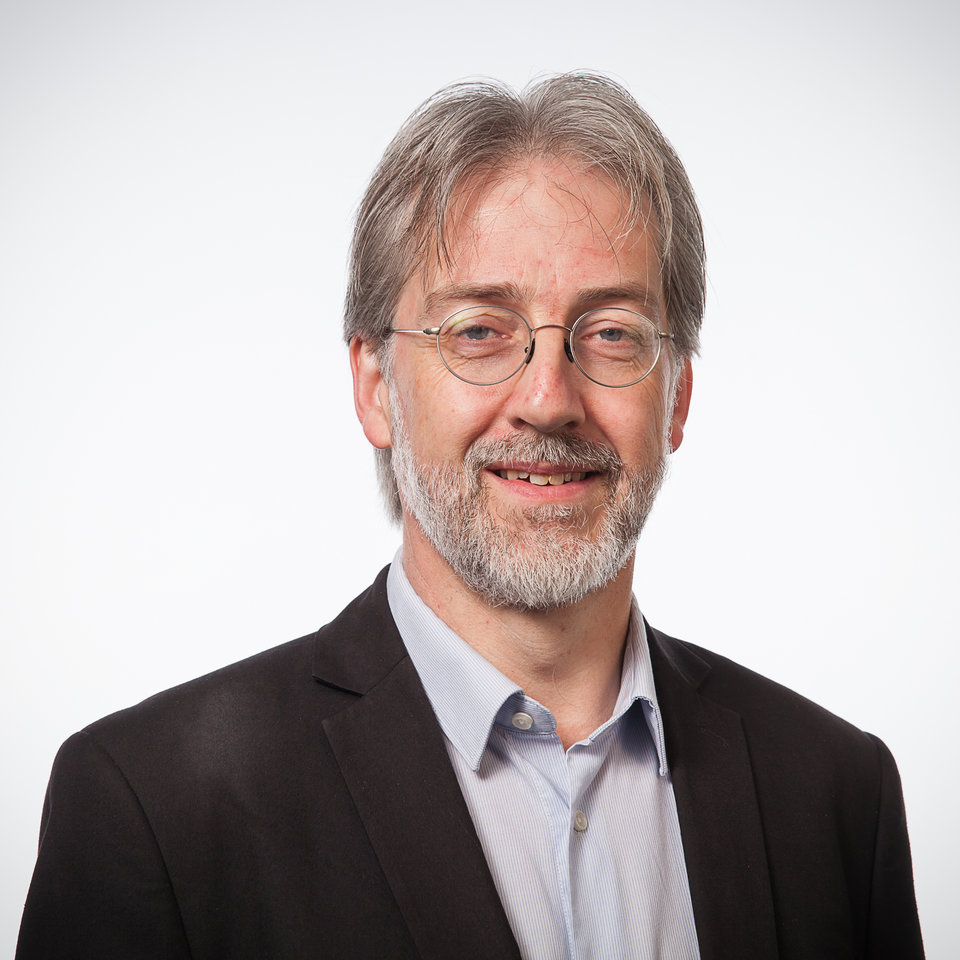
Hans Goosen
TU DelftPhD / PostDoc
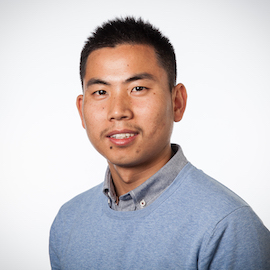
Qi Wang
PostDoc researcher, TU Delft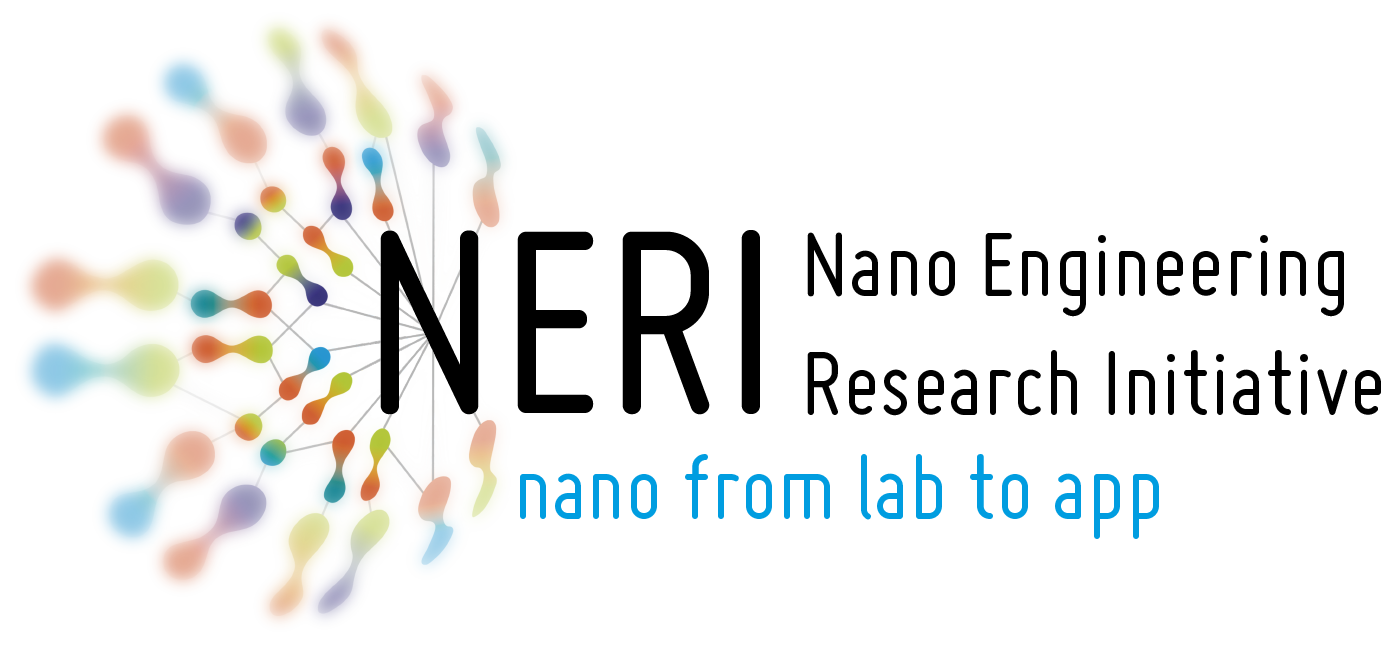