CL-Windcon
Background
Wind farms (or: wind plants) are a multitude of turbines placed in each other’s proximity. Placing turbines together has a number of benefits, such as
- reduced deployment costs of the electricity grid,
- reduced land- or sea-use and visual pollution,
- increased power capture per unit area at resource-rich locations/topologies.
However, grouping turbines in farms also has several complications that negatively impact the performance and lifetime of the turbines. These complications arise due to interactions between turbines through their wakes, which are slower, more turbulent wind structures induced by energy extraction of the turbine rotor. Turbines operating in the wake of an upstream turbine capture less power and experience higher structural loading.
Though, these complications are neglected in the current control methodology of turbines inside a wind farm. Specifically, a greedy control approach is followed, where each turbine maximizes its own power capture, neglecting its impact on other turbines through its wake. More recently, coordinated wind farm control algorithms which account for these wake effects have shown significant potential in increasing the power production and reducing the loads of downstream turbines.
Currently, the wind farm control community has mainly focused on feedforward control approaches, in which a simple steady-state model is used to determine the optimal control settings for each turbine. However, these approaches neglect all temporal dynamics, and furthermore are limited by their model’s accuracy. However, due to the large time delays in the dynamics of this inter-turbine coupling, the large uncertainties in the environment, and the complicated dynamics on a wide range of spatial and temporal scales inside wind, no surrogate models exist that are accurate, at least not consistently (for varying wind speeds, directions, atmospheric conditions, …).
Goal of this project
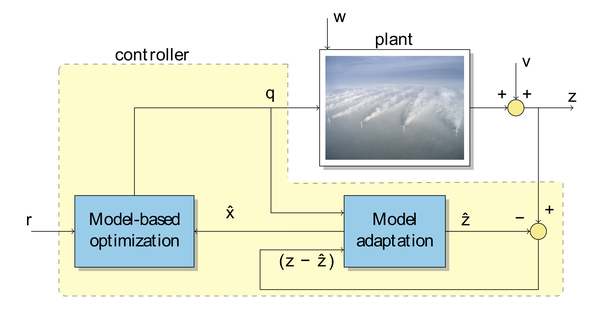
In the CL-Windcon project, we move towards the closed-loop control paradigm, where surrogate models are calibrated online. This will allow the synthesis of accurate and robust closed-loop control algorithms that push the limits of wind farm performance (high power capture, low structural loading).
More formally, the CL-Windcon project contains four goals:
1. Technical: develop closed-loop wind farm control algorithms and improve the understanding of wake interactions inside a wind farm.
2. Economical: evaluate the economic worth of the new wind farm control algorithms to maximize potential payoffs coming from the new technology
3. Environmental: evaluate the overall value chain through a life cycle assessment.
Social: create green business opportunities and jobs, set design standards, foster the european competitiveness and increase the public acceptance of wind energy.
Work programme
The project is subdivided into 7 so-called “work packages”:
- Wind farm control-oriented model development
In this work package, we analyse the current body of literature on surrogate wind farm models. We trade off the existing control-oriented wind farm models, and make a selection. We will validate these models using high-fidelity simulation software, and then use these models for controller synthesis. - Wind farm flow control technologies and algorithms
The control models from the first work package are used for wind farm controller synthesis is this package. Specifically, this project is aimed at closed-loop controller synthesis, thus with online model calibration using measurements obtained online from the turbines in the wind farm. Furthermore, this project includes the synthesis of supporting technologies, such as local wind turbine control algorithms that work in harmony with the supervisory wind farm control algorithms. - Demonstration and validation of prototypes
The control algorithms from work package 2 are tested at three levels of realism. Firstly, high-fidelity simulation data will be used as a first step of validation. Secondly, a subset of control algorithms will be tested in the wind tunnel at the Politecnico di Milano. Thirdly, one or two wind farm control algorithms will be tested in a real-life scenario at the Sedini wind farm in Italy. - Feasibility
A complete cost-benefit analysis will be performed, among others, to determine the feasibility of the control algorithms and their implementation on existing and future wind farms. - IPR, exploitation, dissemination and communication of results
The findings of this project will be published in the open domain. This includes a website, research articles, open-source code repositories, among others. - Management
Progress and technical reports are published to highlight the progress of the project. - Ethics requirements
The project is performed according to the ethics requirements of the European Union.
For a more elaborate description of the project, please visit the CL-Windcon website at http://www.clwindcon.eu/.
Outcome
B. M. Doekemeijer, S. Boersma, L. Y. Pao and J. W. van Wingerden, "Ensemble Kalman filtering for wind field estimation in wind farms," 2017 American Control Conference (ACC), Seattle, WA, 2017, pp. 19-24. doi: 10.23919/ACC.2017.7962924
S. Boersma, B.M. Doekemeijer, P.M.O. Gebraad, P.A. Fleming, J. Annoni, A.K. Scholbrock, J.A. Frederik, and J-W. van Wingerden, "A Tutorial on Control-Oriented Modeling and Control of Wind Farms", 2017 American Control Conference (ACC), Seattle, WA, 2017, pp. 1-18. doi: 10.23919/ACC.2017.7962923
S. Boersma, B.M. Doekemeijer, M. Vali, J. Meyers and J.W. van Wingerden, "A control-oriented dynamic wind farm model: WFSim", Wind Energ. Sci. Discuss., https://doi.org/10.5194/wes-2017-44, in review, 2017.
B.M. Doekemeijer, S. Boersma, L. Y. Pao, T. Knudsen, J. W. van Wingerden, (2018) Online model calibration and state estimation for a simplified LES model in pursuit of real-time closed-loop wind farm control. Wind Energ., in review.
Wind field estimation in pursuit of closed-loop wind farm control
Description: the video shows the online calibration of a dynamic wind farm model. This online calibration algorithm can be used in combination with a control algorithm to find the optimal control policy inside the wind farm. Specifically, the results presented in the video correspond to the publication from Doekemeijer et al. (2017) at the American Control Conference in Seattle. The dynamic wind farm model is called “WindFarmSimulator”, and is actively being developed at the TU Delft by Boersma et al. Measurements are taken from the high-fidelity simulation code (SOWFA) behind the turbine rotor (about 2% of the total number of variables), and the remaining 98% of the variables are estimated. The goal is to bring the estimation of WFSim/WFObs as close to that of SOWFA as possible.
The control solutions presented in this video can be downloaded for free at https://github.com/TUDelft-DataDrivenControl/.
Wind field estimation in pursuit of closed-loop wind farm control
Real-time model calibration for wind farm control
Project team members
- ir. Sjoerd Boersma
- ir. Bart Doekemeijer
- ir. Joeri Frederik
- ir. Sebastiaan Mulders
- dr. ir. Jan-Willem van Wingerden
Keywords
Closed-loop, control, wind farm, wind plant, real-time control, estimation, Kalman filtering, predictive control, coordinated control, distributed optimization, model calibration, surrogate modeling, reduced-order models, wind turbine control, derating, wake redirection control, axial induction control, wake steering
Sponsored by:
The CL-Windcon project is funded by the European Union. This project has received funding from the European Union's Horizon 2020 research and innovation programme under grant agreement No 727477.
Partners:
To reach the aforementioned goals, we work together with a number of leading research institutes, universities and industrial companies. The partners are: Centro Nacional de Energias Renovables (CENER), General Electric (GE), ENEL Green Power (EGP), Ramboll, DNV GL, University of Stuttgart, Technical University of Munich (TUM), Energieonderzoek Centrum Nederland (ECN), Politecnico di Milano (POLIMI), Ikerlan-IK4, Aalborg Universitet (AAU), Qi Energy Assessment, and DEWI.