Mechanical behavior of additive manufacture materials
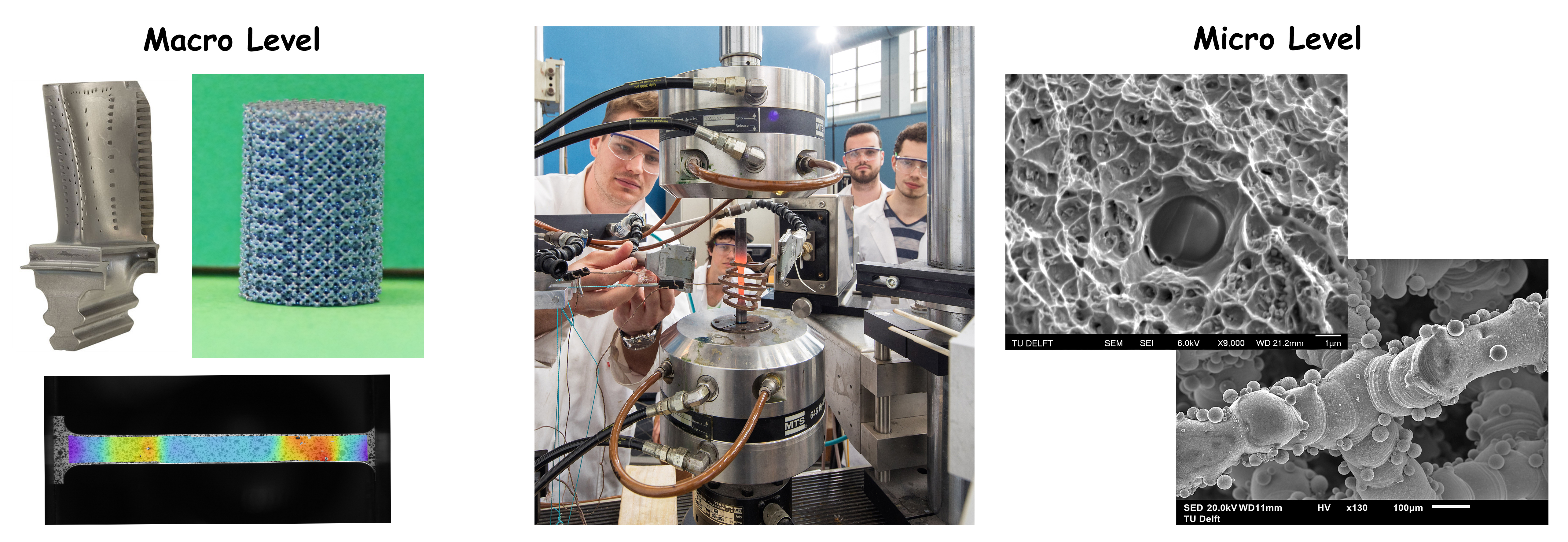
Additive manufacturing technologies such as, for example, selective laser melting (SLM) offer new design possibilities for a wide range of applications and industrial sectors, including aerospace, biomedical and automotive industry. However, the process is characterized by rapid thermal cycles (rapid solidification and fast cooling), resulting in specific microstructures that differ substantially from their cast or wrought counterparts. To make full use of such new materials, their mechanical properties must be characterized and predicted. Hence, the main focus of this research theme is to investigate room and high temperature static and dynamic behaviour of additive manufactured materials. The processing-structure-property (fatigue and fracture)-performance relationships is studied at different length scales.
Current research projects:
B1. Creep and Thermomechanical Fatigue of additive manufactured Inconel components
Inconel 718 is a nickel-based superalloy, which is commonly used in aircraft engine and nuclear applications, where components experience severe mechanical and thermal stresses. Due to the typical high temperature uses, fatigue and creep tests are common benchmarks for such applications. Additive manufacturing offers a unique way of manufacturing Inconel 718 with high degree of design freedom. However, very limited knowledge exists regarding the resulting high temperature properties. The objective of this work is to evaluate creep and thermo-mechanical fatigue (TMF) behaviour of Inconel 718 produced by selective laser melting. The effect of post heat-treatment and resulting microstructures are also evaluated.
B2. Effect of post treatment on fatigue lifetime of Titanium lattice structures
Additive manufactured porous Ti-6Al-4V is considered one of the best candidates for bone replacements due to flow permeability as well as matching stiffness. There are ongoing investigations in order to increase the static mechanical behaviour of porous Ti-6Al-4V samples. However, limited studies available looking into fatigue life of the samples.
The aim of this project is to enhance the fatigue life of porous titanium specimens by development of suitable post-heat treatment and optimization of surface properties.