Dieper ingaan op de volgende generatie implantaten, met drie disciplines tegelijk
Het is al tientallen jaren onbetwist de gouden standaard voor implantaten: titanium: een sterk, licht en corrosiebestendig metaal dat veilig in het lichaam verwerkt kan worden. En toch is er veel te doen over de manier waarop er titaniumimplantaten worden gemaakt. De komst van 3D-printtechnologie heeft aantrekkelijke nieuwe fabricagemogelijkheden geopend. Biomechanisch ingenieurs Dr. Mohammad Ahmadi en Prof. Amir Zadpoor en materiaalkundige Dr. Vera Popovich waren al met deze techniek bezig, zij het op verschillende schaalniveaus. Het leek dus een logische stap om gezamenlijk 3D-geprinte implantaten naar een hoger niveau te tillen, mede geholpen door onderzoeker Dr. Can Ayas van de afdeling Precision and Microsystems Engineering. Het cohesieproject ‘Functional Grading and Microstructural Design of Porous Titanium Produced by Additive Manufacturing’, dat de disciplines nu gedrieën ondernemen, moet de basis leggen voor een grotere samenwerking.
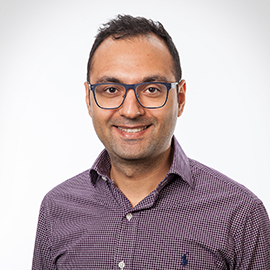
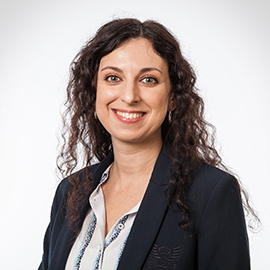
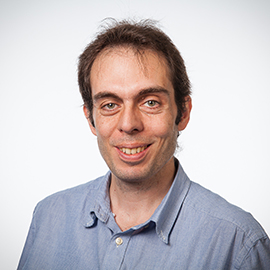
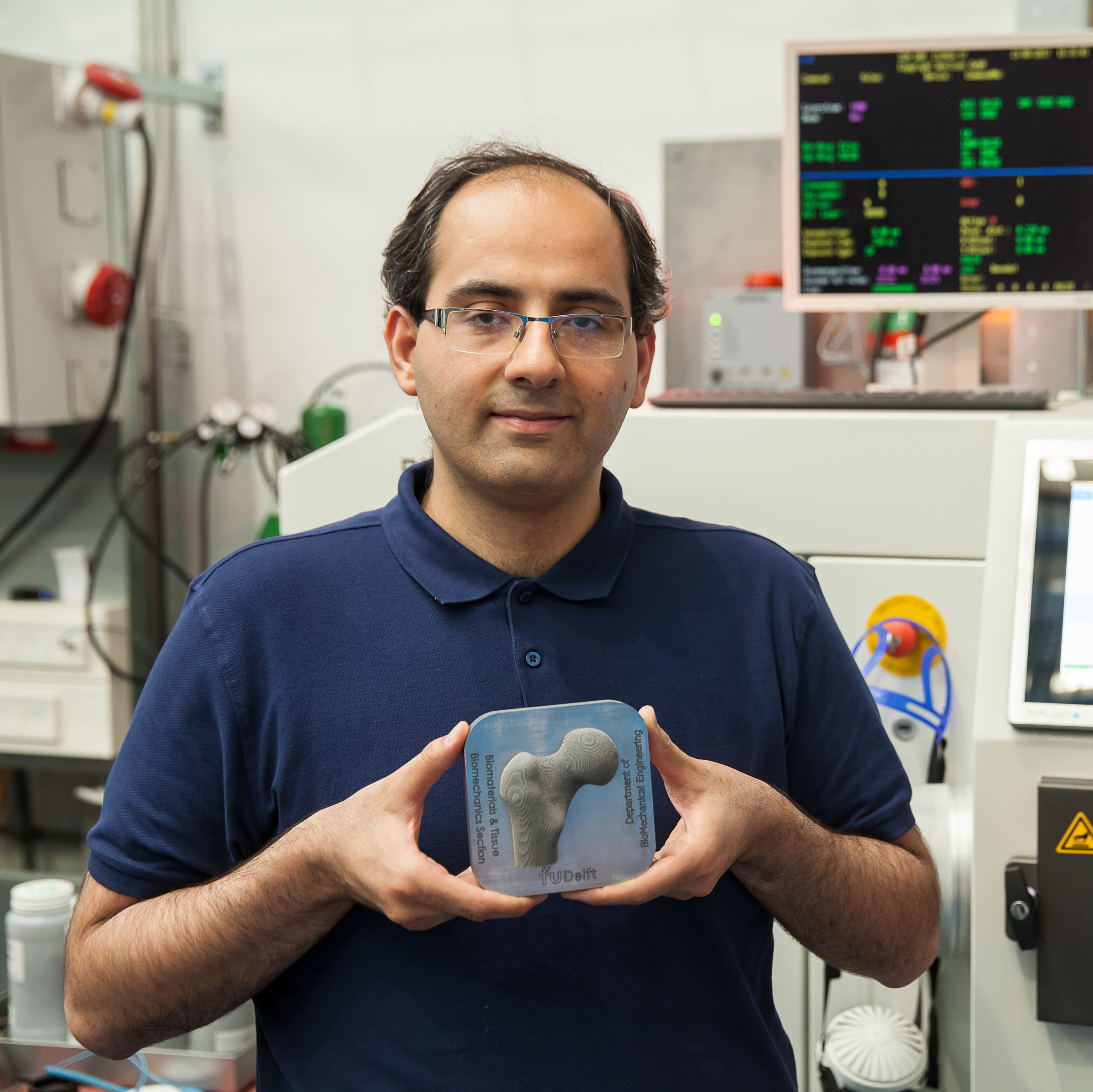
De keten van micro naar macro sluiten
Nadat het idee was geboren om gezamenlijk de keten van ‘micro’ naar ‘macro’ te sluiten, vond het team in biomechanisch ingenieur Ahmadi de persoon om het cohesieproject uit te voeren. Eerder onderzocht hij hoe de 3D-printinstellingen de macroscopische eigenschappen van dit nieuwe type implantaat bepalen. De logische vervolgvraag was in hoeverre de microstructuur (1 micrometer = 1 miljoenste meter) ook invloed heeft op de macroscopische eigenschappen van implantaten, zoals sterkte en levensduur. Deze vraag proberen Ahmadi en het multidisciplinaire samenwerkingsverband nu te beantwoorden. Maar hoe sturen drie kapiteins één schip? Popovich: ‘De belangrijkste factor voor het slagen van een cohesieproject als de onze is een onderzoeker te vinden met ervaring en enthousiasme over het project en de samenwerking.’
Poreus titaan
Waar draait het project om? ‘3D-geprinte implantaten op basis van titaniumlegeringen zijn wat mij betreft de toekomst,’ vertelt Ahmadi. ‘Het zijn op bot lijkende poreuze structuren die goed met natuurlijke botstructuren geïntegreerd kunnen worden.’ Door de mate van porositeit te variëren, proberen wetenschappers de materiaaleigenschappen van de implantaten zoveel mogelijk te laten lijken op die van natuurlijk bot. Titanium en legeringen ervan zijn nou eenmaal een stuk stijver en zwaarder dan bot; dat verschil kan in de praktijk tot problemen leiden. Daarnaast kan het botmateriaal indringen tot in de poriën van de poreuze titaniumstructuur, wat gunstig is voor de aansluiting van het implantaat op het bot. Na de eerdere optimalisatie van de vorm en afmetingen van de poriën, neemt het cohesieproject nu de volgende stap: het verbeteren van de eigenschappen van het implantaat door de microstructuur slim te ontwerpen en het oppervlak van de titaanmatrix op micrometerniveau te optimaliseren.
Veelbelovende resultaten
De onderzoekers zijn zich terdege bewust van de tijdsdruk: ‘Een cohesieproject duurt maar een jaar; dat is wat kort om de ambities te realiseren die bij aanvang gesteld zijn.’ Popovich bouwde dan ook snel een team en netwerk op: het project wordt nu ondersteund door een gastonderzoeker, een afstudeerstudent en partners in Gent en van universiteiten in St. Petersburg. Samen combineerden ze twee technieken om de poreuze titaanmatrix te optimaliseren: hot isostatic pressing zorgt ervoor dat het materiaal waaruit de matrix bestaat zelf minder poreus wordt zonder de essentiële poriën ertussen te aan te tasten; zandstralen op microniveau maakt het materiaaloppervlak van de matrix gladder en beter bestand tegen scheuren. ‘Dit is de eerste keer dat de microstructuur van 3D-geprinte voorwerpen op deze manier geoptimaliseerd is.’ De resultaten zijn veelbelovend: het titaan kent na optimalisatie minder metaalmoeheid en structuren die op dezelfde wijze zijn geproduceerd, vertonen minder variatie dan zonder de optimalisatiestap. ‘Dat zijn allebei belangrijke voordelen op weg naar het gebruik van 3D-printen voor het grootschalig produceren van betere en veiligere implantaten,’ aldus Popovich. De resultaten leidden al tot twee publicaties. ‘Hierna willen we graag kijken naar het effect van de optimalisatiestap op het vermogen van bot om op het titaanoppervlak te groeien.’
Geslaagd huwelijk
Op dit moment werkt het team op laboratoriumschaal. In de komende jaren willen de onderzoekers komen tot een prototype op grotere schaal. De weg naar een product dat daadwerkelijk in de medische praktijk gebruikt kan worden, is notoir lang. Het vereist de nodige certificatiestappen en overtuigingskracht richting artsen. Ook de kosten spelen een rol. Popovich: ‘De fabricagemethode door middel van 3D-printen is nu misschien nog duurder, maar de markt is sterk in beweging. 3D-printen wordt al grootschalig gedaan binnen de luchtvaartsector en auto-industrie, en voor specifieke medische toepassingen. De printers zullen meer en meer betaalbaar en onmisbaar worden.’ Naast het fundamentele onderzoek dat het team doet richt het zich op de korte termijn op het vinden van fondsen voor een groter onderzoeksprogramma waarin de genoemde disciplines structureel samenwerken. ‘Ons cohesieproject is een ambitieus plan dat voortbouwt op lopend onderzoek aan de deelnemende afdelingen.’ Een geslaagd huwelijk van vakgebieden noemt Popovich het. En hopelijk het begin van een langdurige samenwerking.
‘Met dit cohesieproject willen we het fundament leggen voor een grootschalig multidisciplinair onderzoeksprogramma naar betere en veiligere implantaten.’
‘Ons project is een ambitieus plan dat voortbouwt op lopend onderzoek aan de deelnemende afdelingen. Het is een geslaagd huwelijk van vakgebieden en hopelijk het begin van een langdurige samenwerking.’
3mE Cohesieprojecten
Cohesieprojecten zijn in 2014 gestart vanuit een idee van decaan Theun Baller met als doel interdisciplinaire samenwerking binnen de faculteit te stimuleren. Een goede ingenieur is immers bij uitstek een samenwerker en de meeste innovaties ontstaan op het snijvlak van disciplines. De cohesieprojecten geven jonge onderzoekers de mogelijkheid om funding aan te vragen voor projecten, met als voorwaarde samenwerking met collega’s binnen de faculteit en buiten de eigen discipline. In een grote faculteit als 3mE kon de samenwerking wel een duwtje gebruiken. Inmiddels worden de successen geoogst: Werktuigbouwkunde, Maritieme Techniek en Materiaalkunde lenen zich uitstekend voor onverwachte cross-overs met verrassende uitkomsten